The Single Strategy To Use For Alcast Company
The Single Strategy To Use For Alcast Company
Blog Article
Some Known Incorrect Statements About Alcast Company
Table of ContentsThe Best Guide To Alcast CompanyThe Alcast Company PDFsThe smart Trick of Alcast Company That Nobody is DiscussingAbout Alcast CompanyAlcast Company Fundamentals ExplainedRumored Buzz on Alcast Company
Chemical Comparison of Cast Aluminum Alloys Silicon promotes castability by minimizing the alloy's melting temperature level and enhancing fluidity throughout spreading. Furthermore, silicon adds to the alloy's stamina and put on resistance, making it important in applications where resilience is critical, such as automotive parts and engine elements.It likewise improves the machinability of the alloy, making it easier to refine right into ended up products. In this method, iron contributes to the overall workability of light weight aluminum alloys.
Manganese adds to the strength of light weight aluminum alloys and boosts workability. Magnesium is a lightweight aspect that gives strength and impact resistance to aluminum alloys.
How Alcast Company can Save You Time, Stress, and Money.
Zinc boosts the castability of light weight aluminum alloys and assists manage the solidification process throughout spreading. It boosts the alloy's strength and firmness.
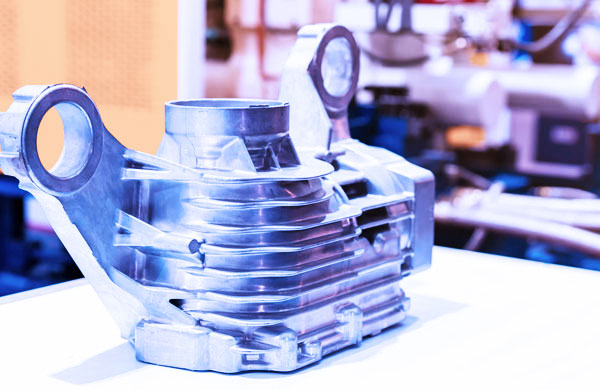
The primary thermal conductivity, tensile strength, yield strength, and elongation differ. Among the above alloys, A356 has the highest thermal conductivity, and A380 and ADC12 have the least expensive.
How Alcast Company can Save You Time, Stress, and Money.
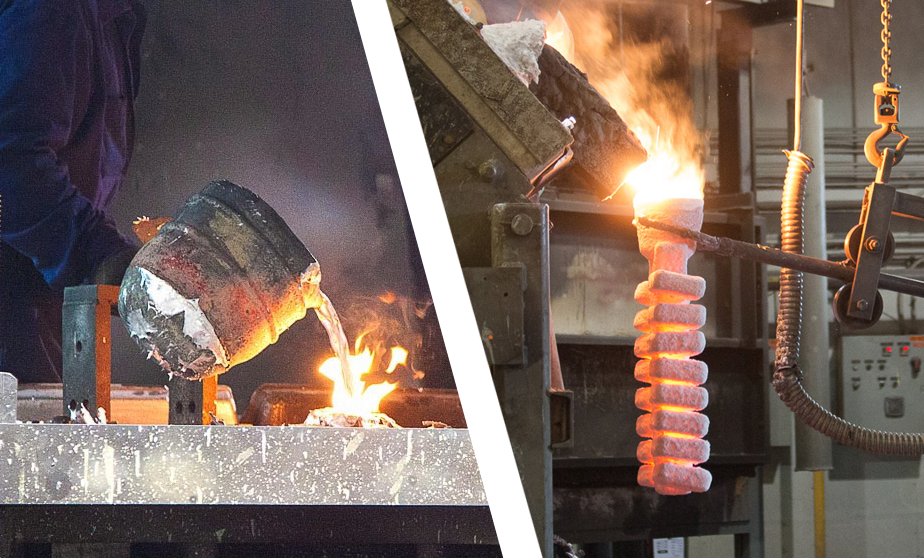
In accuracy casting, 6063 is well-suited for applications where detailed geometries and top notch surface area finishes are vital. Instances consist of telecommunication rooms, where the alloy's superior formability enables for streamlined and cosmetically pleasing designs while maintaining structural honesty. In the Illumination Solutions market, precision-cast 6063 elements produce classy and efficient lights components that call for elaborate forms and excellent thermal efficiency.
It leads to a better surface finish and far better deterioration resistance in A360. The A360 exhibits premium prolongation, making it perfect for facility and thin-walled components. In accuracy spreading applications, A360 is fit for markets such as Customer Electronic Devices, Telecommunication, and Power Devices. Its improved fluidness enables elaborate, high-precision parts like smartphone coverings and communication device housings.
The Of Alcast Company
Its distinct residential properties make A360 a useful choice for accuracy spreading in these markets, enhancing item resilience and top quality. Aluminum alloy 380, or A380, is a widely used casting alloy with several unique attributes. It uses superb castability, making it a perfect option for precision casting. A380 shows excellent fluidness when molten, making certain intricate and in-depth mold and mildews are precisely recreated.
In accuracy spreading, aluminum 413 shines in the Consumer Electronics and Power Equipment sectors. It's typically made use of to craft intricate parts like mobile phone housings, camera bodies, and power device casings. Its precision is exceptional, with tight resistances up to 0.01 mm, guaranteeing perfect item setting up. This alloy's exceptional corrosion resistance makes it an excellent selection for outdoor applications, making sure long-lasting, sturdy items in the stated sectors.
Some Known Questions About Alcast Company.
The light weight aluminum alloy you select will significantly affect both the casting process and the homes of the last item. Since of this, you must make your choice thoroughly and take an enlightened strategy.
Identifying the most suitable light weight aluminum alloy for your application will certainly imply considering a wide selection of attributes. The first classification addresses alloy characteristics that check here impact the production process.
Alcast Company - An Overview
The alloy you select for die casting directly influences several facets of the casting process, like how easy the alloy is to deal with and if it is prone to casting flaws. Hot breaking, additionally recognized as solidification cracking, is a typical die spreading problem for light weight aluminum alloys that can cause interior or surface-level rips or cracks.
Specific light weight aluminum alloys are more susceptible to warm breaking than others, and your selection should consider this. It can harm both the cast and the die, so you should look for alloys with high anti-soldering properties.
Corrosion resistance, which is currently a notable characteristic of aluminum, can vary significantly from alloy to alloy and is an essential characteristic to consider depending on the environmental conditions your product will certainly be exposed to (Foundry). Put on resistance is another residential property generally looked for in light weight aluminum products and can differentiate some alloys
Report this page